Precision die making
From the signing of precision mold manufacturing orders to the delivery of qualified mold to customers every link may affect the quality of the mold, precision mold manufacturing process according to the system engineering control, every link must be controlled, is the premise of precision mold manufacturing.
The guiding principle of mold parts processing is to make corresponding process plans for different mold parts, different materials, different shapes and different technical requirements. The general technological process of mold parts is: blank preparation - rough machining - semi-finishing machining - heat treatment (quenching and tempering) - precision grinding - electrical machining - fitter finishing and surface machining. Through the control of each process, the required machining accuracy is achieved.
1. Materials and heat treatment control
Mould parts heat treatment to make parts needed to get the material hardness at the same time, and to make the parts after machining process and stable size shape, according to the characteristics of different parts of materials and parts structure has different way of heat treatment, must to control stress in heat treatment of parts to make heat treatment process, we must give full consideration to the material hardenability hardenability heat-sensitive and decarburization sensitivity, to adopt pressure quenching process of thin-walled parts.
(1) Selection of precision die materials: in addition to CrWMn, Cr12, 40Cr, GCr15, Cr12MoV and 9Mn2V hard alloy, alloy steel S2, S3, V10, APS23S1, G2, G3, G4 and G8 can be selected for some die and punch with high working strength and severe stress.
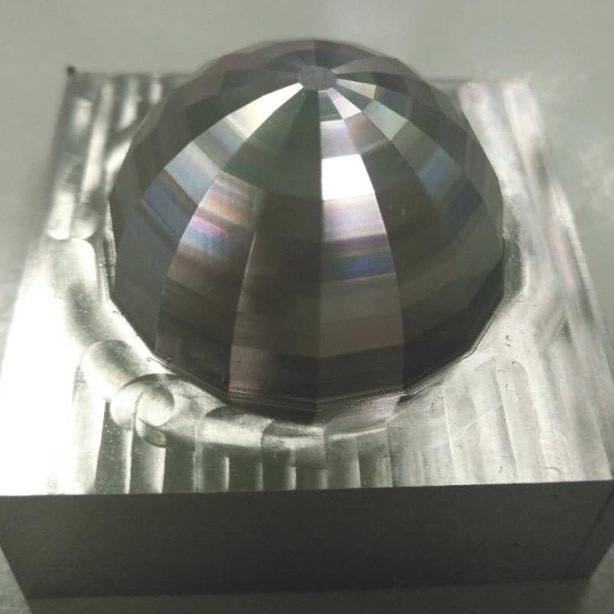
(2) to deal with the stress after quenching, quenching after the artifacts are kept stress, easy to cause the follow-up after finishing workpiece size change even cracking, so the parts should be hot after quenching tempering, eliminate the quenching stress on complex shape, inner and outer corner more artifacts, tempering is not sufficient to eliminate the quenching stress, still need to go before finishing annealing or aging treatment for many times, fully release the stress.
2. Edm control
(1) Preparation for wire cutting: Precision slow-moving wire cutting machine tool is selected for wire cutting, with processing precision ±0.001mm and roughness Ra=0.2um. The perpendicularity of deionized water wire cutting wire with high degree of deionization meets the requirements of processing precision. The material of wire used for proper tensioning force cutting is suitable for the material of the workpiece to be cut to ensure a reasonable processing speed.
(2) the processing route design: wire-cutting processing on the material of the original stress balance is destroyed in the process of machining, cause stress concentration around the corner, processing method of stress concentration, by using the principle of the vector translation, finish machining allowance for 0.8 ~ 0.9 mm, before rehearsals cavity rough shape, and then to heat treatment, machining stress release before finishing, as far as possible to ensure that the thermal stability. 4 times of cutting shall be adopted in the processing of punch. The cutting wire cutting position and path shall be reasonably determined and the clamping blank position shall be selected after the first feeding. The workpiece shall not be in the state of suspension after the first feeding, and the workpiece shall always be in a good stress state without affecting the subsequent processing. Perforating the blank and threading the wire, the processing effect is better than the shape cutting.
(3) EDM forming process: Rough and fine electrodes should be made in EDM forming process respectively. Fine electrode is machined by CNC CNC machine, cu-W alloy electrode has good comprehensive performance, and the electrode loss is very small compared with that of red copper. Under good chip removal conditions, it is difficult to process materials and parts with complex cross section shapes. Ag-w alloy electrode has better performance than Cu-W alloy electrode, which can be used in precision machining. Graphite electrode is made of imported graphite with small loss, high hardness, fast electric erosion and low surface roughness. Before the end of EDM, fine gauge finishing is arranged to remove the hardened thin layer formed on the surface.
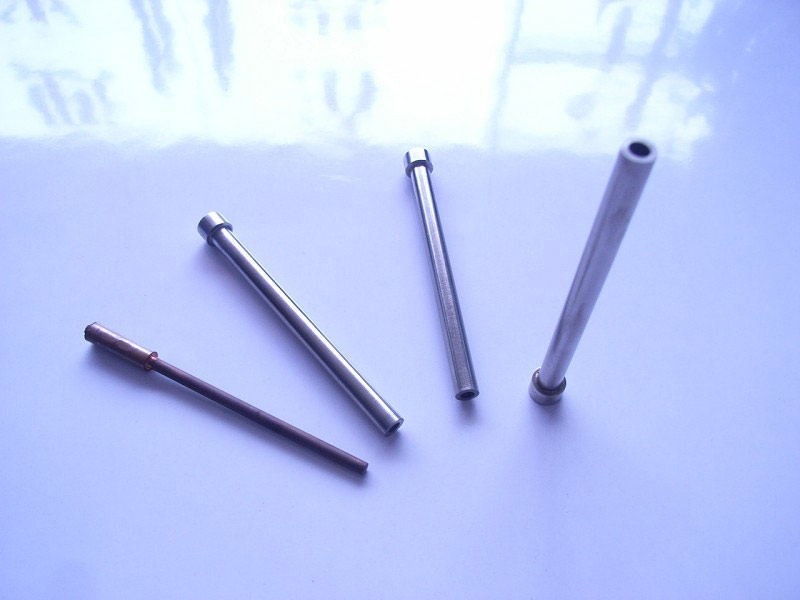
Dongguan Pengle precision components Co., Ltd. is a mobile phone precision mold manufacturing, processing, manufacturers. Over the past 15 years, Pengle has continuously introduced advanced technology and equipment from Germany and Japan, established a unique standardized quality control center, recruited and trained talents who have been focusing on mobile phone board and mobile phone precision accessories for more than 10 years, optimized THE ISO management mode, and built a modular, transparent and modern factory with unique style in the industry.
From the signing of precision mold manufacturing orders to the delivery of qualified mold to customers every link may affect the quality of the mold, precision mold manufacturing process according to the system engineering control, every link must be controlled, is the premise of precision mold manufacturing.
The guiding principle of mold parts processing is to make corresponding process plans for different mold parts, different materials, different shapes and different technical requirements. The general technological process of mold parts is: blank preparation - rough machining - semi-finishing machining - heat treatment (quenching and tempering) - precision grinding - electrical machining - fitter finishing and surface machining. Through the control of each process, the required machining accuracy is achieved.
1. Materials and heat treatment control
Mould parts heat treatment to make parts needed to get the material hardness at the same time, and to make the parts after machining process and stable size shape, according to the characteristics of different parts of materials and parts structure has different way of heat treatment, must to control stress in heat treatment of parts to make heat treatment process, we must give full consideration to the material hardenability hardenability heat-sensitive and decarburization sensitivity, to adopt pressure quenching process of thin-walled parts.
(1) Selection of precision die materials: in addition to CrWMn, Cr12, 40Cr, GCr15, Cr12MoV and 9Mn2V hard alloy, alloy steel S2, S3, V10, APS23S1, G2, G3, G4 and G8 can be selected for some die and punch with high working strength and severe stress.
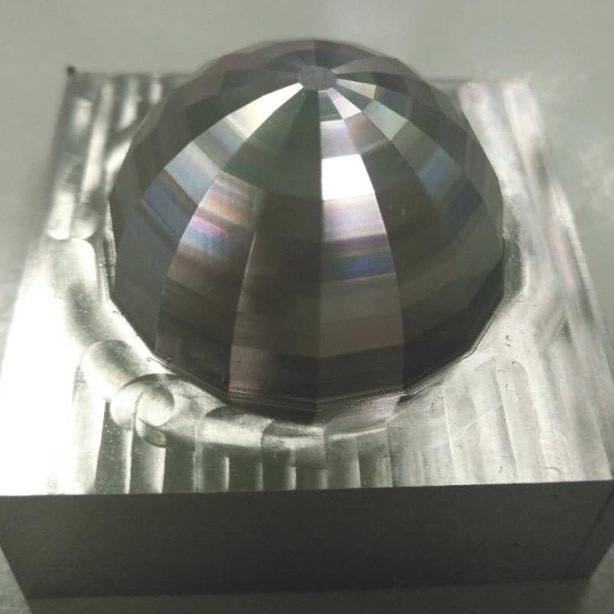
2. Edm control
(1) Preparation for wire cutting: Precision slow-moving wire cutting machine tool is selected for wire cutting, with processing precision ±0.001mm and roughness Ra=0.2um. The perpendicularity of deionized water wire cutting wire with high degree of deionization meets the requirements of processing precision. The material of wire used for proper tensioning force cutting is suitable for the material of the workpiece to be cut to ensure a reasonable processing speed.
(2) the processing route design: wire-cutting processing on the material of the original stress balance is destroyed in the process of machining, cause stress concentration around the corner, processing method of stress concentration, by using the principle of the vector translation, finish machining allowance for 0.8 ~ 0.9 mm, before rehearsals cavity rough shape, and then to heat treatment, machining stress release before finishing, as far as possible to ensure that the thermal stability. 4 times of cutting shall be adopted in the processing of punch. The cutting wire cutting position and path shall be reasonably determined and the clamping blank position shall be selected after the first feeding. The workpiece shall not be in the state of suspension after the first feeding, and the workpiece shall always be in a good stress state without affecting the subsequent processing. Perforating the blank and threading the wire, the processing effect is better than the shape cutting.
(3) EDM forming process: Rough and fine electrodes should be made in EDM forming process respectively. Fine electrode is machined by CNC CNC machine, cu-W alloy electrode has good comprehensive performance, and the electrode loss is very small compared with that of red copper. Under good chip removal conditions, it is difficult to process materials and parts with complex cross section shapes. Ag-w alloy electrode has better performance than Cu-W alloy electrode, which can be used in precision machining. Graphite electrode is made of imported graphite with small loss, high hardness, fast electric erosion and low surface roughness. Before the end of EDM, fine gauge finishing is arranged to remove the hardened thin layer formed on the surface.
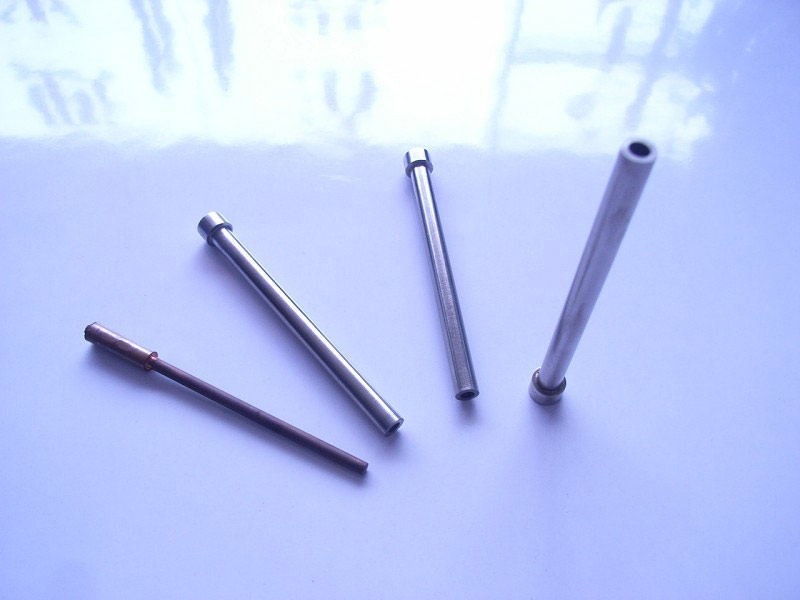